Next Generation Open Architecture Offering Will Streamline Processes, Advance Digital Quality Workflows & Enable Additive Industry Users to Gain Consistency Across Their Sites and Supply Chains
Sigma Additive Solutions, Inc. (NASDAQ: SASI) ("Sigma", "we," "our," or the "Company"), a leading developer of quality assurance software to the commercial 3D printing industry, announced today that it is releasing a beta version of the PrintRite3D® Machine Health module. This new solution marks the beginning of the company’s software-only approach to quality assurance by allowing users to take disparate machine log files and standardize them. Built upon Sigma’s PrintRite3D monitoring and analytics technology, the company is creating a framework for connecting and standardizing distinct sensors and images into a cohesive product suite.
This press release features multimedia. View the full release here: https://www.businesswire.com/news/home/20221103005528/en/
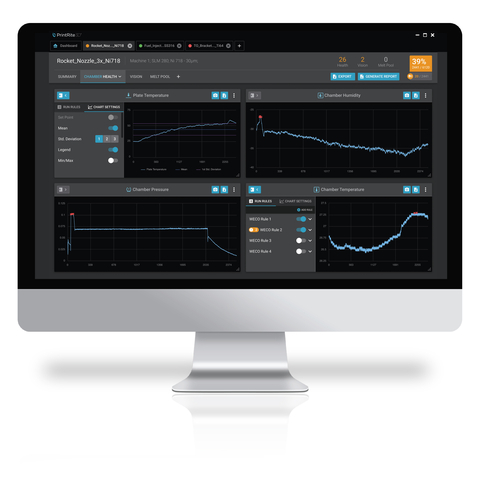
Machine Health from Sigma Additive Solutions (Graphic: Business Wire)
Features of the new solution include:
- A path to scale for integrated sensor fusion of camera, thermal camera, melt pool data, and more
- Ability to link machines by API or upload all machine sensor .csv log files
- Creation of a common standards-based file format for analytics, visualization, and reporting, agnostic of machine type
- A single cohesive environment for all in-process quality data, customizable to unique production requirements
- Deep insight, analytics, and reporting of machine sensor data
- Dashboard visualization showing key metrics
“This is an exciting announcement, not only for Sigma, but for the entire additive industry,” remarked Jacob Brunsberg, Sigma’s President and Chief Executive Officer. He added, “Today, proprietary quality control approaches of various additive machine manufacturers often lead to inconsistency in quality assurance across manufacturing operations. The objective of the initial module, and all future modules, is to help drive a standards-based approach to additive manufacturing, allowing users to gain consistency across their sites and supply chains. Allowing users to take disparate machine log files and standardize them is an important first step in connecting distinct sensors and images into a cohesive product suite.”
“A truly holistic approach to quality is just what the industry needs,” stated Ivan Madera, Chief Executive Officer of Morf3D. “As a member of the Sigma Additive Product Advisory Council, I am thrilled to have early access to the launch of the Machine Health and future modules, and to put them to work in our facility. Standardizing machine logs will streamline processes and advance digital quality workflows. Having a single interface, streaming data from all connected machines, moves the industry forward into a digital future and away from hours of work from manually collecting, converting, processing, and analyzing all the individual aspects of quality.”
Darren Beckett, CTO of Sigma, added “Sensor fusion – conjoining data types – will provide improved confidence in defect detection, root cause analysis and mitigation, allowing everyone to interpret control charts and other data types/sources uniformly. Our engineering team has spent over 10 years developing the technology to provide a framework for standards-based data exchange, metrics, and analytics. We are committed to an open architecture philosophy and acting as a third-party agnostic option, connectable to the broader installed base of the additive industry.”
About Sigma Additive Solutions
Sigma Additive Solutions, Inc. is a leading provider of in-process quality assurance (IPQA™) solutions to the additive manufacturing industry. Sigma specializes in the development and commercialization of real-time monitoring and analytics known as PrintRite3D® for 3D metal and polymer advanced manufacturing technologies. PrintRite3D detects and classifies defects and anomalies real-time during the manufacturing process, enabling significant cost-savings and production efficiencies by reducing waste, increasing yield and shortening cycle times. Sigma believes its software solutions will be a major catalyst for the acceleration and adoption of industrial 3D printing. For more information, please visit www.sigmaadditive.com.
Forward-Looking Statements
This press release contains "forward-looking statements" within the meaning of Section 27A of the Securities Act of 1933, as amended, and Section 21E of the Securities Exchange Act of 1934, as amended. Statements preceded by, followed by or that otherwise include the words "believe," "anticipate," "estimate," "expect," "intend," "plan," "project," "prospects," "outlook," and similar words or expressions, or future or conditional verbs such as "will," "should," "would," "may," and "could" are generally forward-looking in nature and not historical facts. These forward-looking statements involve known and unknown risks, uncertainties and other factors. Among the important factors that could cause actual results to differ materially from those indicated by such forward-looking statements are risks relating to, among other things, market and other conditions, Sigma’s business and financial condition, the extent of the market's acceptance of PrintRite3D®, Sigma’s ability to satisfy its capital needs through increasing its revenue and obtaining additional financing, and general economic, industry or political conditions in the United States or internationally. Sigma disclaims any intention to, and undertakes no obligation to, revise any forward-looking statements, whether as a result of new information, a future event, or otherwise. For additional risks and uncertainties that could impact Sigma’s forward-looking statements, please see disclosures contained in Sigma's public filings with the SEC, including the "Risk Factors" in Sigma's Annual Report on Form 10-K, which may be viewed at www.sec.gov.
View source version on businesswire.com: https://www.businesswire.com/news/home/20221103005528/en/
Contacts
Chris Tyson
Executive Vice President
MZ Group - MZ North America
949-491-8235
SASI@mzgroup.us
www.mzgroup.us